Leading Benefits of Hiring Specialists for Welding Inspection Madison
Leading Benefits of Hiring Specialists for Welding Inspection Madison
Blog Article
Discovering Advanced Equipment and Methods for Accurate Welding Inspection
In the realm of welding inspection, the pursuit of precision and dependability is paramount, stimulating the advancement of innovative devices and approaches. Laser scanning innovations and automated assessment systems, equipped with man-made knowledge, are redefining the landscape by reducing human mistake and improving safety and security steps.
Ultrasonic Examining Technologies
Ultrasonic testing innovations frequently represent the forefront of developments in welding assessment modern technologies. These developments have actually considerably enhanced the capacity to identify and examine suspensions within bonded structures, making certain improved stability and safety and security.
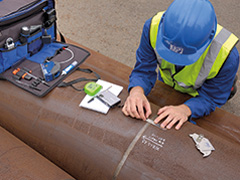
In addition, advancements in software program algorithms for data evaluation have actually improved the accuracy of defect discovery and sizing. Automated ultrasonic testing systems currently provide high-resolution imaging, enabling comprehensive evaluations of weld top quality. These systems are often incorporated with innovative visualization devices, which promote the analysis of results.
Radiographic Evaluation Methods
While ultrasonic screening advancements have actually established a high criterion in non-destructive assessment, radiographic assessment strategies continue to play an essential role in welding inspection by providing special insights right into material honesty. Radiographic testing (RT) uses the usage of X-rays or gamma rays to permeate materials, developing a radiograph that aesthetically stands for the internal structure of a weld. This imaging capability is vital for spotting subsurface defects such as porosity, inclusions, and cracks that may not be visible via surface assessments.
The procedure includes putting a radiation resource on one side of the weld and a detector on the opposite side. Variants in material thickness and thickness affect the attenuation of the rays, generating a different photo that specifically delineates imperfections. RT is specifically useful for examining thick sections and complex geometries where various other techniques may drop short.
Regardless of its effectiveness, radiographic evaluation should be carried out with rigorous adherence to safety protocols because of the hazardous nature of ionizing radiation. Moreover, the interpretation of radiographs requires knowledgeable personnel, as the high quality of the evaluation straight affects the reliability of the examination. As a result, continuous advancements in digital radiography are boosting photo clearness and analysis effectiveness, strengthening RT's critical function in making sure weld top quality.
Laser Scanning Breakthroughs
Embracing laser scanning technology in welding assessment has actually revolutionized the evaluation of weld high quality and honesty. Unlike typical evaluation strategies, laser scanning offers rapid data acquisition, significantly improving the efficiency and precision of weld evaluations.
Laser scanning developments have led to substantial enhancements in defining and discovering surface problems such as porosity, lack of combination, and undercuts. The high-resolution data enables assessors to perform detailed analyses, ensuring that welds meet rigorous industry standards. Furthermore, this method sustains the advancement of digital documents, facilitating lasting high quality guarantee and traceability.
In addition, laser scanning technology integrates effortlessly with software options made for automated defect detection page and evaluation. The resultant information can be quickly shared and reviewed, promoting collective decision-making procedures. As sectors remain to require greater criteria for weld quality, laser scanning stays at the forefront, using unmatched accuracy and performance in welding assessment.
Automated Assessment Solutions
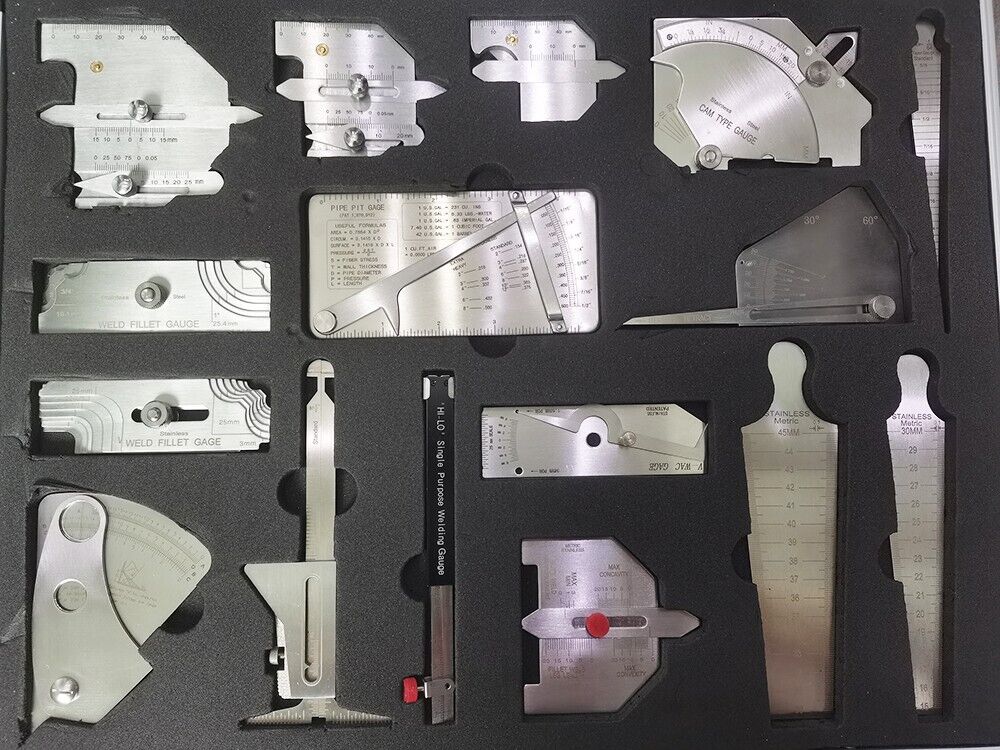
Automated evaluation systems provide the advantage of consistency, removing human error and subjectivity from the evaluation procedure. They are developed to run in numerous atmospheres, from manufacturing floors to remote field websites, ensuring detailed coverage. Welding Inspection Madison. These systems can be set to stick to specific welding standards and requirements, giving thorough records and documents for quality assurance objectives
Additionally, the integration of cloud-based platforms assists in the storage and evaluation of large amounts of evaluation information. This enables fad analysis and anticipating upkeep, enabling suppliers to resolve possible issues before they rise. The pop over here fostering of automated examination systems is a crucial step in the direction of improving the dependability and efficiency of welding procedures in industrial applications.
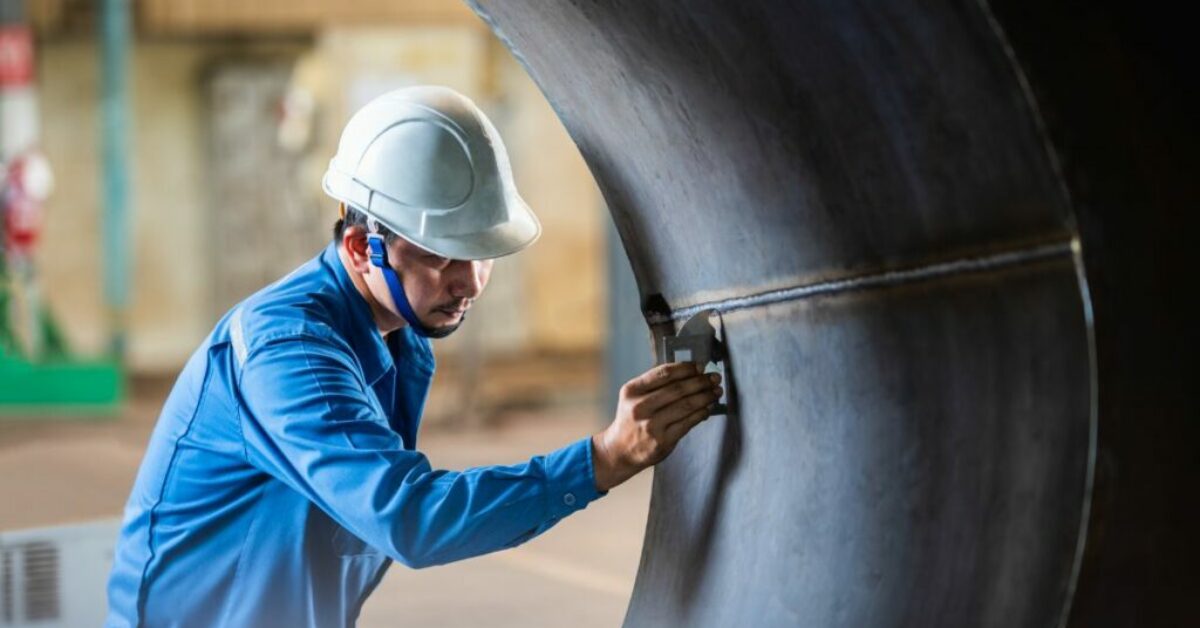
Enhancing Safety And Security and Effectiveness
A significant facet of enhancing safety and performance in welding assessment hinges on the assimilation of ingenious innovations that simplify procedures and minimize threats. The fostering of advanced non-destructive testing (NDT) methods, such as ultrasonic screening, phased variety ultrasonic screening (PAUT), and radiographic screening, plays a crucial duty in making sure architectural stability without endangering the security of the personnel entailed. These strategies allow for extensive assessments with marginal downtime, lowering potential risks related to conventional approaches.
Moreover, the implementation of real-time data analytics and machine discovering algorithms has transformed the means evaluation information is translated. By employing predictive analytics, possible defects can be recognized prior to they manifest into vital failures, ensuring timely interventions and upkeep. This aggressive approach considerably boosts operational effectiveness and security in welding procedures.
Moreover, remote evaluation technologies, including drones and robotic spiders equipped with high-resolution cams, enable examiners to examine hard-to-reach areas without subjecting them to hazardous conditions. This not only improves assessment accuracy however also decreases human threat. By leveraging these innovative devices and approaches, markets can achieve higher safety standards and operational efficiency, eventually leading to more lasting and trustworthy welding inspection techniques.
Final Thought
The integration of sophisticated devices and approaches in welding examination considerably improves issue detection and makes certain architectural honesty. These advancements not only increase inspection effectiveness however likewise contribute to enhanced safety and security and quality guarantee in industrial welding applications.

Ultrasonic testing technologies frequently stand for the leading edge of developments in welding assessment modern technologies.While ultrasonic screening innovations have actually established a high standard in non-destructive examination, radiographic evaluation methods proceed to play an essential role in welding examination by using unique insights into material stability.Accepting laser scanning technology in welding inspection has transformed the analysis of weld quality and stability. As markets continue to require higher criteria for weld top quality, laser scanning continues to be link at the center, offering unmatched precision and efficiency in welding evaluation.
Automated evaluation systems supply the benefit of uniformity, eliminating human mistake and subjectivity from the examination procedure.
Report this page